Ready to find out more?
Drop us a line today for a free quote!
WHAT IS PEKK?
PolyEther Ketone Ketone (PEKK) resins are high performance thermoplastics that offer an outstanding combination of material properties not limited tomechanical strength, chemical resistance, low flammability, and high use temperature. PEKK is a member of the Polyaryletherketone (PAEK) family of ultra-high performance polymers, which includes PEEK. However, PEKK is a copolymer, which allows a tunable melt temperature and crystallization rate. PEKK has the extreme performance of a PAEK, but with reduced processing challenges and excellent layer adhesion.
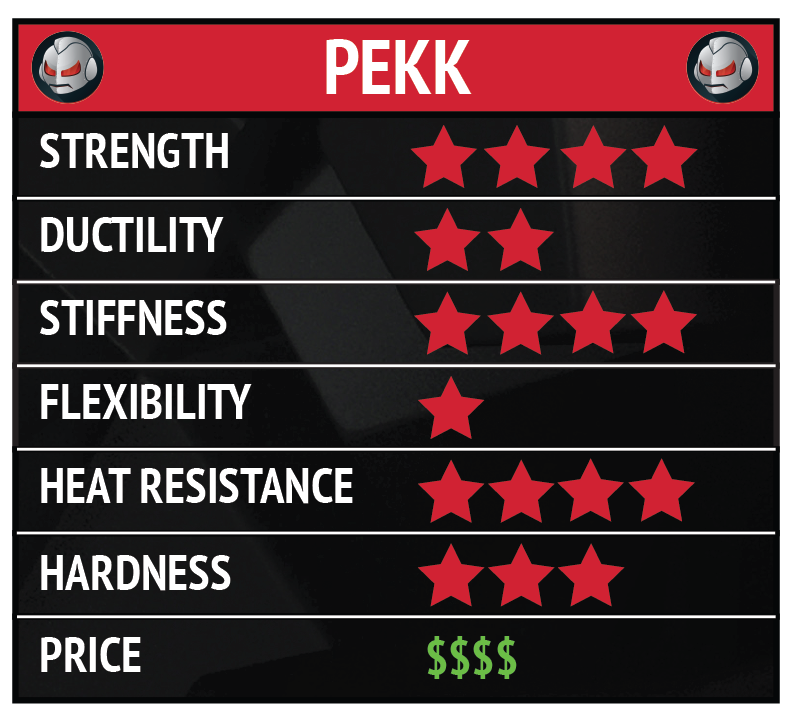
If you are thinking of printing in polyetherimide (PEI/Ultem®), polyphenylsulfone PPSU, or PEEK, PEKK is an alternative that can offer easier processing and better properties.
PEKK Applications
PEKK is primarily used when you need to get the absolute maximum performance from your printed parts. It has a great combination of strength, toughness, chemical resistance, and low flammability. Many of the original applications for PEKK were for metal and thermoset composite replacements in aerospace, but additive manufacturing enables many other small scale applications where other polymer materials are not up to the task.
Applications where PEKK is useful include end-use components exposed to fuels, acids, and lubricants. PEKK may also be used as a replacement for metal products, where applicable, offering light-weight advantages, including:
- Brackets and clips
- Ducts, housings, and under-hood components
- Custom tooling and fixtures

PEKK Performance Features
PEKK, like all PAEKs has an excellent combination of thermal, mechanical, electrical and physical properties making it a truly high performance material. In FFF, we tend to highlight:
- Outstanding mechanical, wear, and impact properties
- Inherent flame resistance, low smoke generation, low outgassing
- Excellent resistance to virtually all organic or inorganic chemicals
- High dielectric strength and good insulating properties
- Easy to process- minimal part warping and modest print conditions
- Possible to produce either amorphous or semicrystalline parts

PEKK Material Properties
PEKK has excellent mechanical properties when printed by fused filament fabrication (FFF). The table below describes some of the mechanical properties possible when printed under optimum conditions. In all cases the tensile specimens were machined from a three millimeter thick box [by Arkema]. Testing was performed in accordance with ASTM standards.
PEKK is intrinsically flame retardant and will meet most flammability requirements for almost any thickness. The base materials in PEKK filaments pass UL V0 requirements as well as standards for aircraft and train interiors.
PEKK is incredibly chemically resistant. In its semi-crystalline form, it resists almost all organic and inorganic chemicals with the exceptions of some very strong acids or extremely aggressive solvents at elevated temperatures. In its amorphous form, PEKK has superior chemical resistance to PEI or PPSU including improved environmental stress cracking resistance.
PEKK is commonly sold as either “amorphous” or semi-crystalline. Amorphous grades are limited in use temperature to about 140°C, and should not be used in the most extreme chemical environments. Semi-crystalline grades require either a high temperature build environment printer or post processing to fully crystalize the material and unlock the absolute best in thermal and chemical resistance properties.
The data below is provided by Arkema for their Kepstan 3D printing filament. Data represents typical values for 3D printed test specimens made from amorphous PEKK, unless otherwise stated.
- Tensile Stress at Break (XY Direction): 85 – 100 MPa
- Tensile Stress at Break (Z Direction): 48 – 65 MPa
- Tensile Modulus (XY Direction): 2,500 - 3,200 MPa
- Tensile Modulus (Z Direction): 1,600 - 2,800 MPa
- Elongation at Break (XY Direction): 6 to 10%
- Elongation at Break (Z Direction): 4 to 6%
- Flexural Strength (XY Direction): 140 MPa
- Flexural Modulus (XY Direction): 3,000 MPa
- Glass Transition Temperature: 160 - 165°C
- Melting Temperature: 300 - 335°C
- Heat Deflection Temperature (1.8 MPa): 139°C
- Heat Deflection Temperature (Semi-crystalline, 0.45 MPa) = 250°C
- Density = 1.27 g/cc
Disclaimer: The above information is provided in good faith. JuggerBot 3D assumes no obligation or liability for the accuracy or completeness of the information supplied in this document. It is solely the customers responsibility to determine if the product and information in this document are appropriate for the customers end use. Responsibility for the use, storage, handling, and disposal of the products herein is that of the purchaser or end user.
PRINTER Requirements AND SETTINGS
For the best results when 3D printing using PEKK, a printer with an enclosed build chamber, a heated bed, and a high temperature capable hot end is highly suggested. According to Arkema, the print conditions that yield the maximum performance from PEKK filament are a build chamber close to Tg , about 150°C and a print temperature of about 360°C. Print speed should be dictated by the level of accuracy required for the part and the capability of the printer you are using. PEKK is compatible with a variety of high temperature soluble and breakaway support materials.
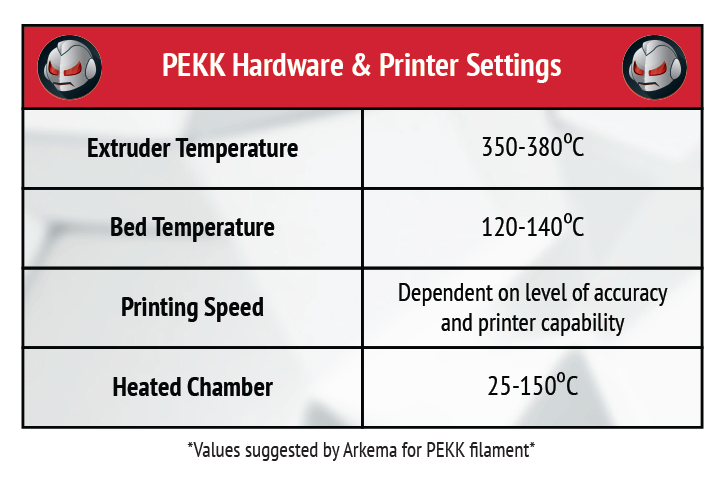
3D Printing with PEKK - the procedure
The build surface for PEKK should either be glass with a glue stick adhesive or a PEI/ PPSU sheet. PEKK has a low tendency to warp during a print, and general good practices to improve build plate adhesion work well for PEKK.
One of the most important rules about processing PEKK by FFF is to start with extremely dry resin PEKK filament should be dried for 8 hours at 120°C before printing, and stored in a desiccated environment for the entire printing process. It is a good idea to dry PEKK even if the spool is brand new in the manufacturer’s sealed bag.
To crystalize PEKK, the final part should immediately be heated to about 200-220°C for about one hour. This will produce a semicrystalline object with excellent layer adhesion and minimal distortion.
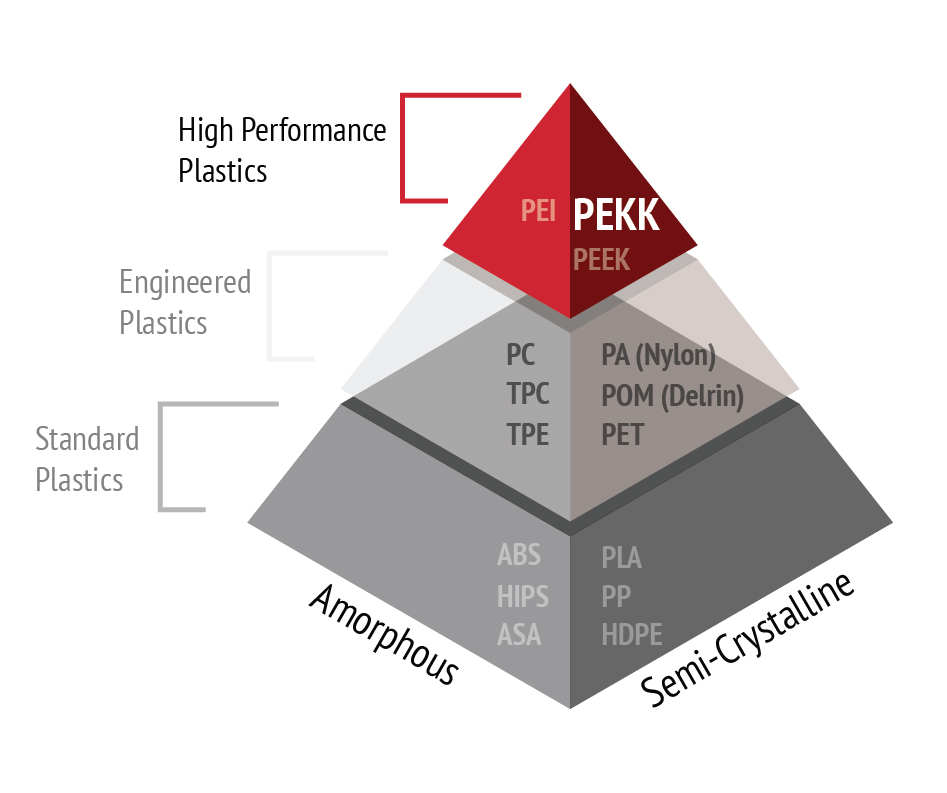

Contributor's Bio:
Roderick Reber is a staff technical service engineer at Arkema Inc. He specializes in additive manufacturing of ultra-high performance polymers, and has nearly a decade of experience working in polymer application development. He holds a BS in Materials Science and Engineering from the Pennsylvania State University, a MS from Drexel University, and an MBA from Villanova University.

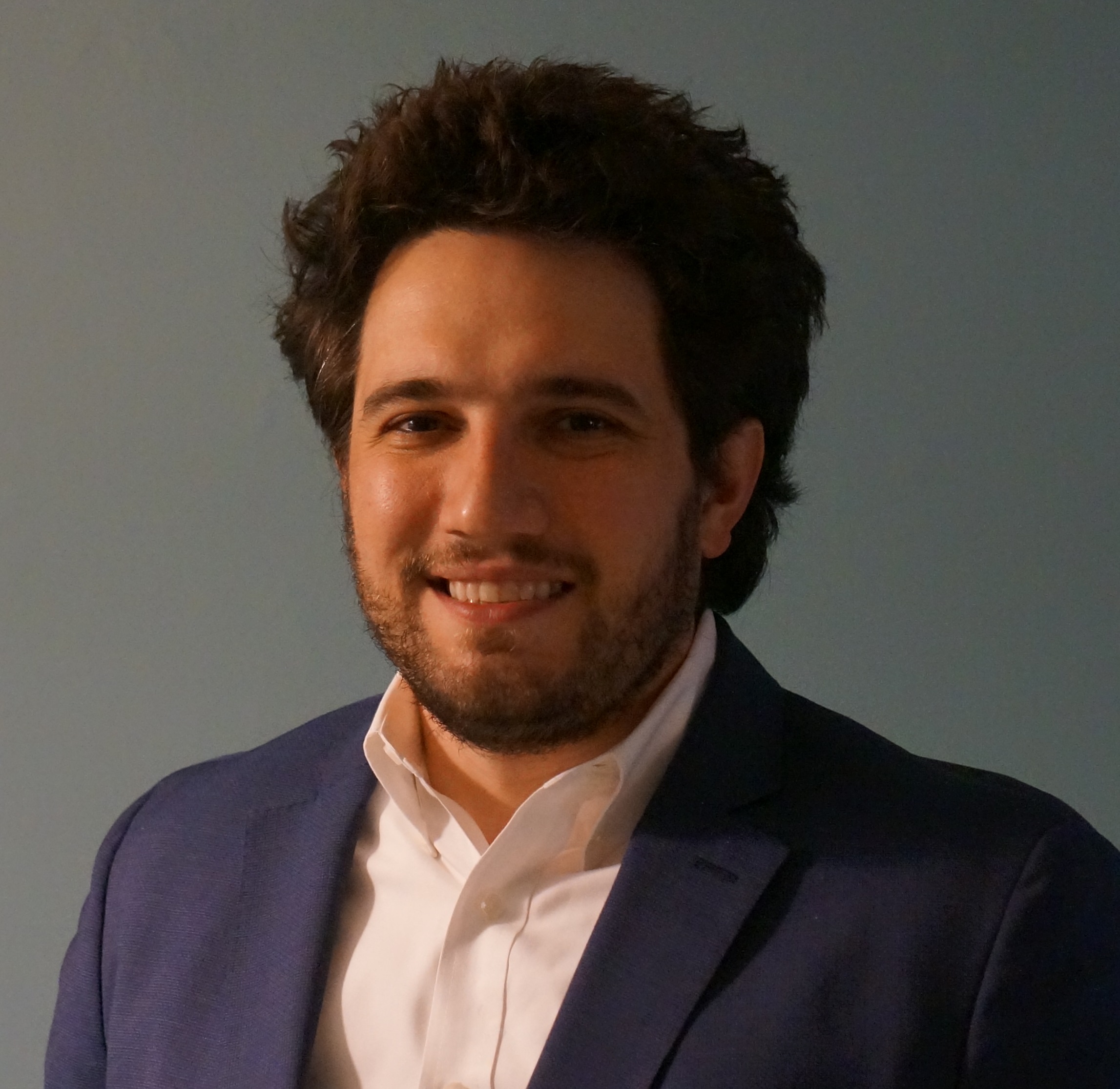