Utilizing JuggerBot 3D’s Bead Characterization System
A single path consisting of multiple legs representing a specific relationship between the material, the machine configuration, and the printing parameters is printed.
The results are then interpreted, either manually or through the use of a laser profilometer, and the “best” leg is selected.
The input of data then proliferates an entire set of parameters, utilizing a proprietary algorithm developed by JuggerBot 3D.
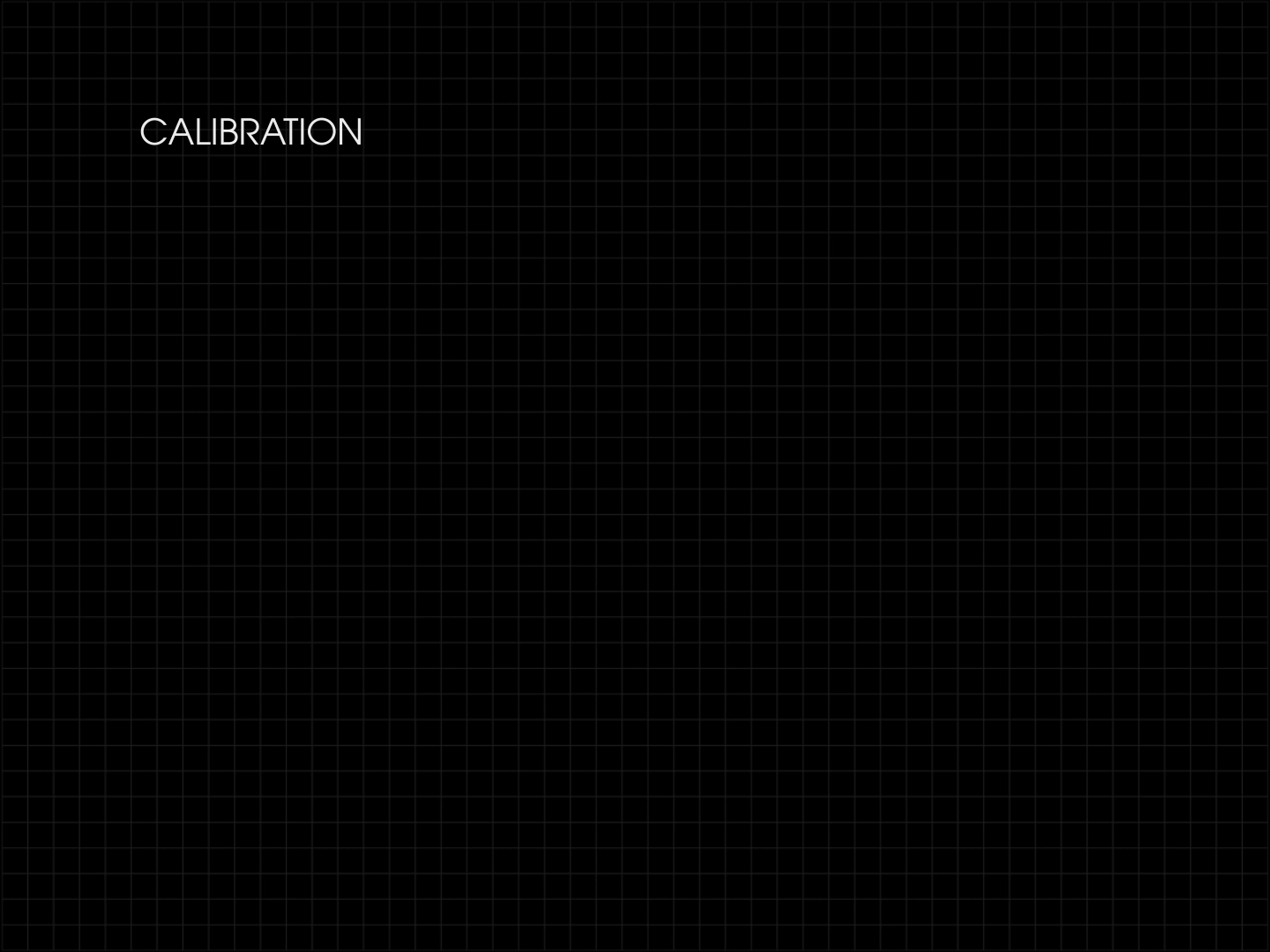