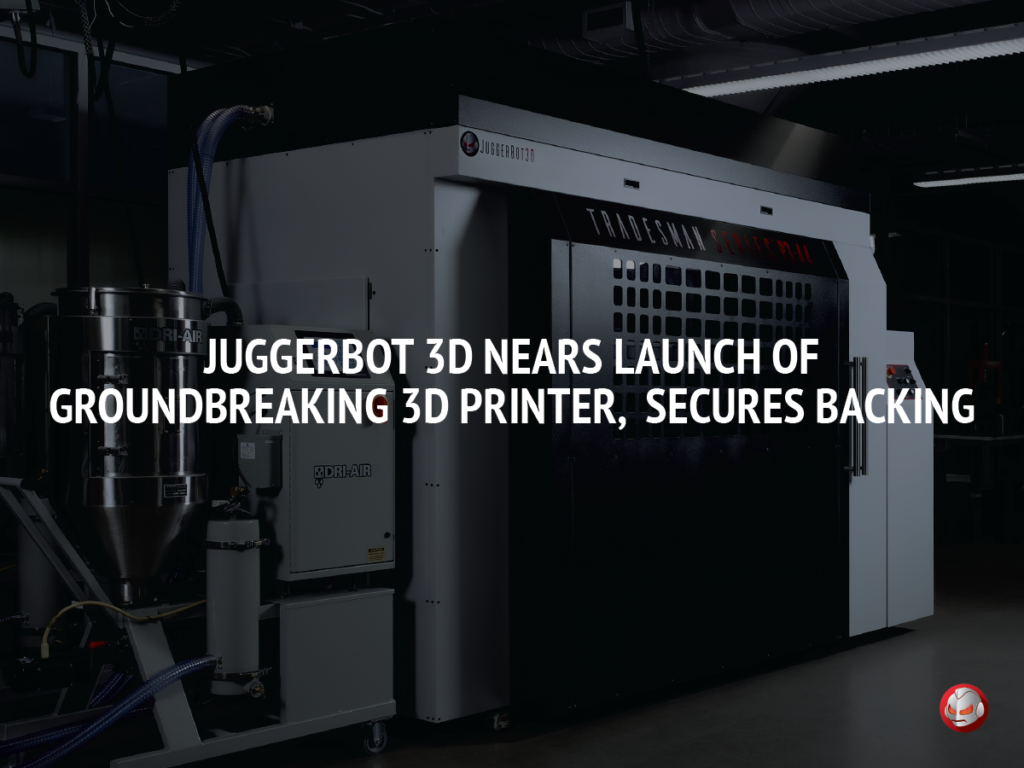
JuggerBot 3D nears launch of groundbreaking 3D printer, secures backing.
JuggerBot 3D nears launch of groundbreaking 3D printer, and secures backing of local businessman.
New technology promises to address 3D printing’s biggest shortcomings in 2020.
Alex Benyo has a little experience building successful manufacturing companies. The Brilex Group of Companies, co-owned by Alex and his brother, Brian, has become one of Youngstown’s fastest growing manufacturing companies.With thriving businesses that specialize in heavy machining and fabrication, welding, and the innovative design and build of OEM industrial equipment, Benyo has an eye for manufacturing technologies that work. Recently, Benyo has decided to include additive manufacturing to that list of technologies by backing JuggerBot 3D.
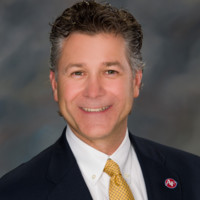
“I am excited about the technology JuggerBot is bringing to the additive market and am blessed to be able to provide a helping hand to this Youngstown gem” exclaims Benyo.
Based in Youngstown, Ohio, JuggerBot 3D started out providing engineering and consulting services to manufacturers in 2014, and in 2018 released a line of industrial-grade 3D printers. This spring, JuggerBot 3D plans to launch a brand-new machine to meet the growing demands of the additive manufacturing industry. The company says it will be the first model in what they call their “Tradesman Series”, built as a compliment for machine tools used across the country to produce patterns, molds, and dies.
“In many ways, our machines can be used where other additive technologies fail to produce parts that either support or work in tandem with CNC machining”, says Dan Fernback, co-founder of JuggerBot 3D. “In many cases, we’ve found that 3D printing can be used to obtain significant cost savings, and also help machinists and patternmakers accomplish more on a daily basis”.
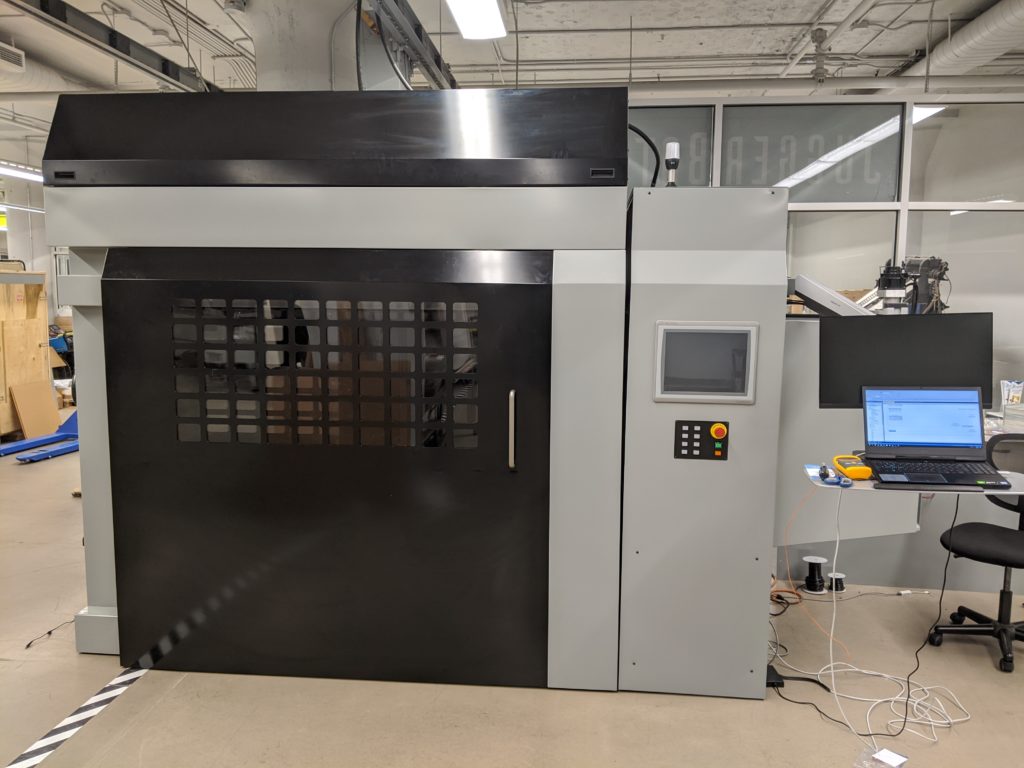
State-of-the-art extrusion technology allows users to drastically increase the printing speeds compared to traditional machines, and enables companies to deliver higher performing parts while reducing material costs. JuggerBot’s new printer can build parts up to three feet in width, four feet in length, and four feet in height, and is uniquely capable of processing performance thermoplastics in pellet form. By doing so, manufacturers can now consider an enormous number of materials that are currently not available for their additive manufacturing applications.
Zac DiVencenzo, co-founder of JuggerBot 3D, believes that pellet extrusion technology is key in advancing additive manufacturing’s value. “With more companies looking at additive to solve their problems than ever before, we are excited to help them tap into new materials that are best fit for 3D printing and their needs”.
JuggerBot 3D’s machines are ‘material agnostic’, meaning that they’re capable of processing various types of thermoplastics from different suppliers. The company believes that it’s essential to work closely with other components of the supply chain.
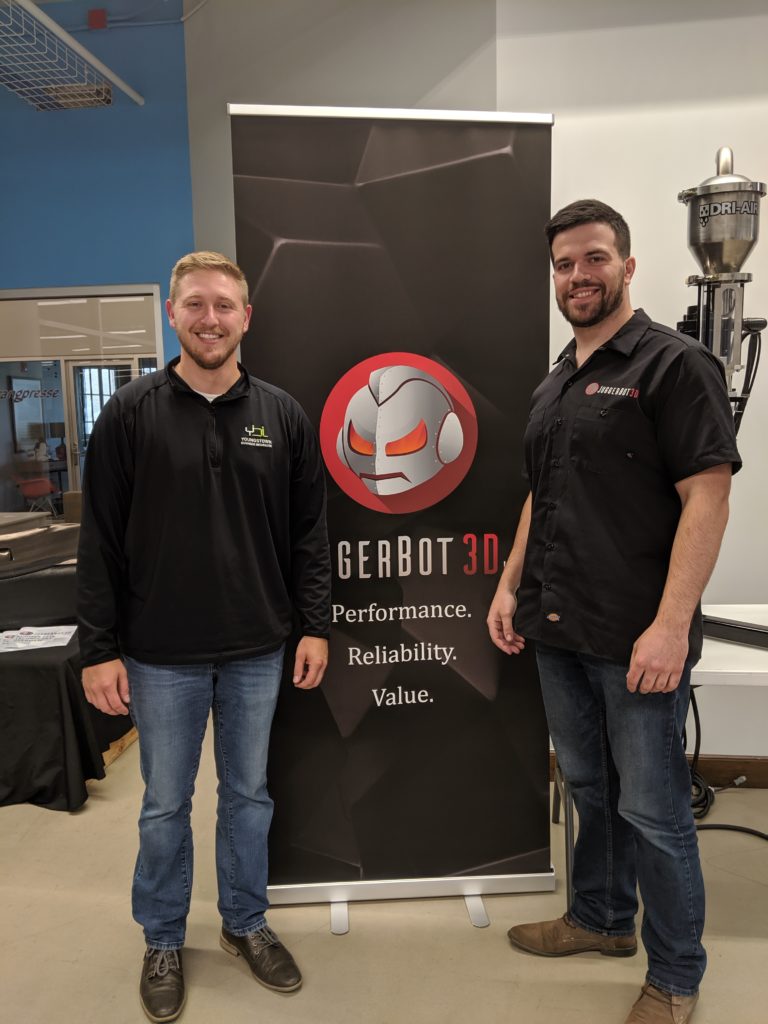
“By aligning with material companies, we are better positioned to respond to our customers’ needs and provide them with the best solution for their application”, says Fernback. “We can focus on being experts with the machines and process, and tap into our partners for material expertise”.
JuggerBot 3D has also established a relationship with Oak Ridge National Laboratory (ORNL), widely known for their ground-breaking development of pellet-extrusion and large format additive manufacturing technology. Notable projects include the world’s first 3D-printed car with Local Motors and a trim-and-drill tool for evaluation by The Boeing Company, which earned ORNL the Guinness World Record for ‘world’s largest solid 3D-printed item’.
In 2019, JuggerBot 3D doubled the amount of space they occupied at the Youngstown Business Incubator, and on-boarded engineers to support the development of their new product line. The company has already received two orders and looks forward to the official launch of their Tradesman Series in the coming months.
JuggerBot 3D will be exhibiting at Metalcasting Congress 2020 in Cleveland this April, and will have parts on display at RAPID+TCT in Anaheim this year.
For more information about JuggerBot 3D’s new machine, please visit our Tradesman Series page, or contact us here.